Identifying materials to combat the cold
Text block one Heading link
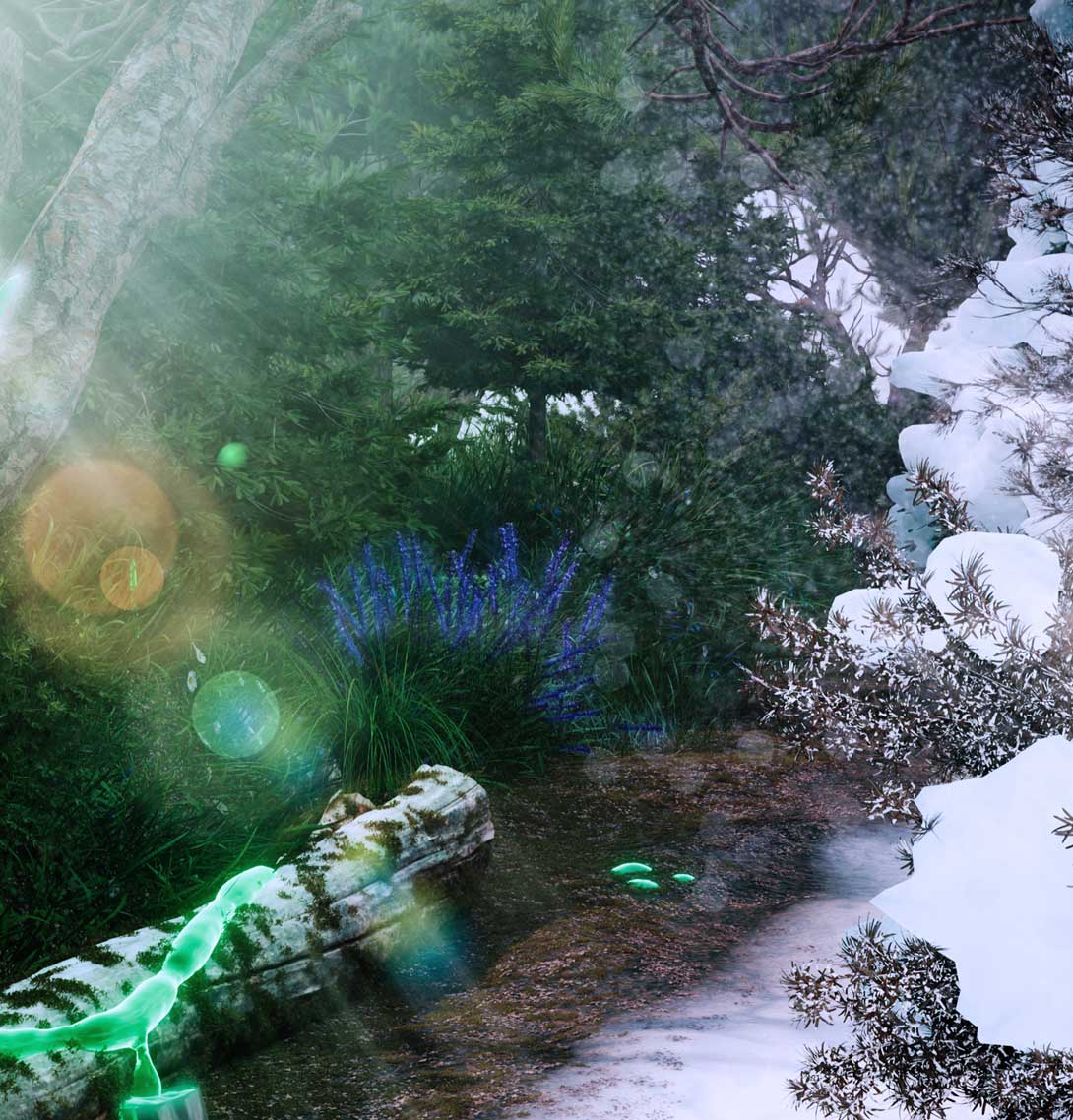
Mechanical and industrial engineering researchers created a design framework for identifying materials out of millions of chemical compounds that can thermally respond by trapping the latent heat released during water vapor condensation and thereby passively delaying the freezing of droplets under frigid temperature conditions.
These materials are substances that release or absorb a significant amount of energy during their phase transition to provide useful heating or cooling applications. Some common examples of phase change materials are water, chocolate, and paraffin waxes. But not every such material can be used for delaying water drop freezing.
To develop the framework, the engineers performed systematic studies to understand the water droplet interactions with various randomly selected phase change materials in the absence or presence of condensation,
The research explains the fundamental mechanisms responsible for condensation-induced melting on a wide variety of phase change materials and demonstrates their versatile real-world applications.
“The coatings are capable of formulation-specific multifunctional properties: frost resistance under frigid conditions, thermoresponsive optical transparency, and fast self-reparability,” Associate Professor Sushant Anand said.
The research has the potential to significantly impact industries such as thermal management, energy storage, and ice-shedding technologies. By using readily available and environmentally safe chemicals, the freeze-protection system sets the groundwork for a greener and more sustainable future.
“PCMs hold tremendous potential toward a myriad of new applications, like the development of anti-freezing storages for vaccines, fog-dew harvesting systems, weather-tolerant wearable electronics, and more,” PhD candidate Rukmava Chatterjee said. “But controlling the supercooling and roughness of PCMs once they turn solid could be the key to getting the best performance out of them, so that is where we are focused next.”